[PR] MG Tech developed a new AMR collaborative mobile robot
“In the context of the development of Industry 5.0, robots are transforming the future work processes. The automation of load movements makes it possible to support operators in improving the skills of their missions. These robots carry out the various tedious and/or repetitive tasks and give operators a better quality of life at work and better availability for operations with higher added value,” explains Eric Gautier, CEO of the MG Tech Group.
Thus, to meet the growing demands of manufacturers, MG Tech has developed and marketed a new AMR collaborative mobile robot (Autonomous Mobile Robot), the EVOBOT.
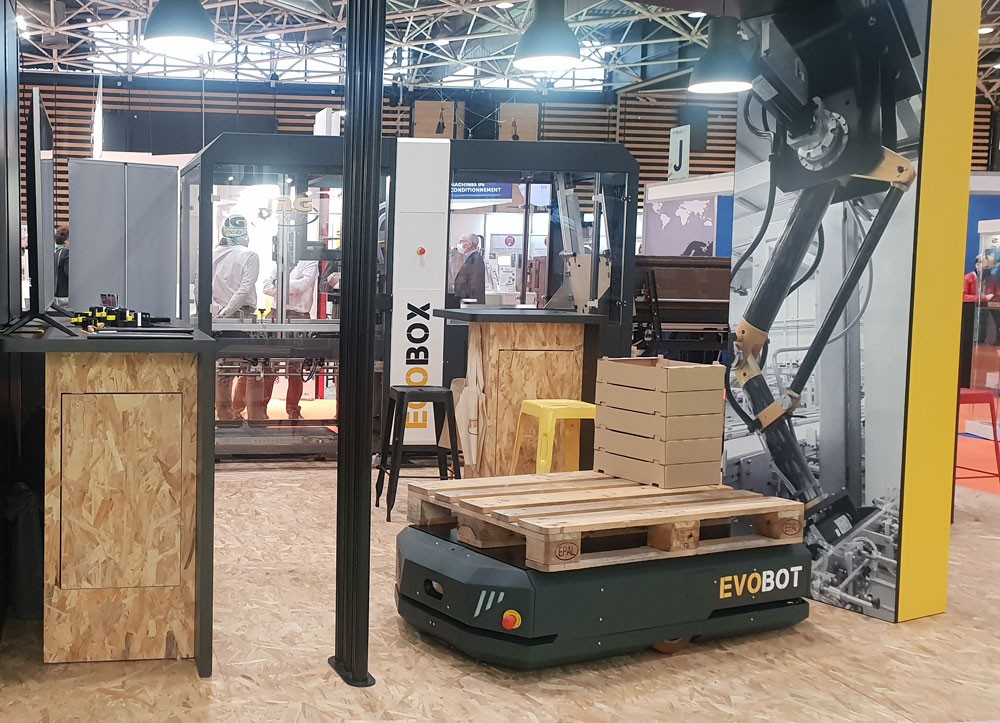
This new autonomous mobile robot is capable of carrying and towing loads of up to 2 tons and 1.5 tons with lifting equipment. Its movement speed can go up to 2 meters per second (7.2 km/h).
The development teams for this new equipment focused on 4 essential criteria, namely: the safety, the navigation system, the energy and the configurations and operations to be carried out.
A perfectly secure mobile equipment
The Evobot robot has two safety lasers, one located at the front right and one at the rear left. These two sensors enable to permanently scan the environment in which the robot evolves, to identify and detect the movements around it and thus to adapt to them. As soon as it detects a person or an object, its movement speed will be reduced or even stopped if necessary.
To guarantee a natural cohabitation between the Evobot robot and humans, the signaling has been particularly studied:
- A set of LEDs signals the start-up and movements
- A blue spotlight is projected on the ground, at the front and at the rear, to signal the arrival of the vehicle
- An audible signal can be setup in a sensitive area.
A complete navigation solution for optimal vehicle control
The Evobot robot comes with a complete navigation solution that calculates the position (simple and reliable localization), controls its movement and can be interfaced directly with the equipment's safety laser scanners.
For each project, the navigation system comes with proven vehicle and mission configuration software.
Our technician intervenes to define the route, recognize the environment, adjust the parameters and check. The transfer of mission data from a computer to a vehicle is done only once. This drastically reduces network requirements (e.g. Wifi).
A maximum autonomy and an automatic recharging system
The AMR Evobot robot is provided with a fully automatic battery charging station. The Evobot can be charged either between each mission or at the end of the exercise, manually (triggered by the operator) or automatically (pre-configured).
Multiple configurations to best suit customer applications
AGV Lifter: the lifter configuration allows to lift and move loads up to 1500 kg. The dimensions of the Evobot enable to transport whole pallets of 1200x800 mm or 1200x1000 mm.
AGV with cobot: placing a cobot arm on a mobile base transforms the robot into a tailor-made solution. This configuration is perfectly suited to small loads, single parts and especially multiple product references.
AGV with tray conveyors: the Evobot is designed to receive one or more tray reception and exit conveyors. Combined with a lift, it will have several reception heights and tray outlets.
AGV with telescopic arm: this equipment is completely adapted to the management of bins with multiple entry and drop-off points.
AGV with pallet conveyors: the Evobot equipped with a pallet conveyor ensures the transfer of pallets from existing conveyors to the AGV (and vice versa).
This autonomous equipment is designed to meet the needs of many sectors of activity (agri-food, logistics, pharmaceutical-cosmetics, industrial, etc.). It will be able to adapt to the constraints of the production environment and to the operators already in place, without ever taking their place but rather by improving their daily lives.